Safety Interlocking for Textile machine
- Home
- Applications
- Door Safety Interlocking
Enquire Now
Let us help you
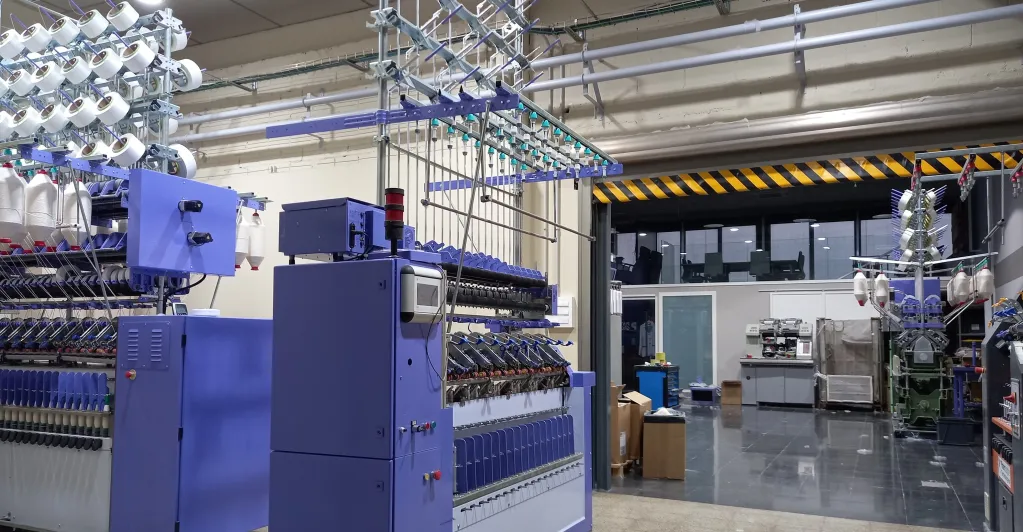
Safety Interlocking for Textile machine
Our sales team has decades of experience in the field finding solutions for our customers’ applications.
- sales@rendertechindia.com
- +91-8698009335
Safety Interlocking for Textile machine
Safety interlocking is essential for the textile industry, where machines such as looms, spinning machines, weaving machines, and dyeing equipment are frequently used in high-speed operations. Given the complexity of these machines and the presence of moving parts, safety interlocks are vital to ensure worker safety and equipment protection. These systems ensure that machines only operate when safe conditions are met, minimizing the risks associated with industrial textile production.
What is Safety Interlocking?
Safety interlocking involves safety devices or systems that prevent machinery from operating unless certain safety conditions are met. These mechanisms can involve safety switches, sensors, or locks that ensure workers are not exposed to hazardous machinery components. For instance, a safety interlock might prevent a machine from starting if its guard or safety cover is not securely in place.
Applications of Safety Interlocking in Textile Machines
- Spinning Machines: Spinning machines are used to convert fibers into yarn. Safety interlocks ensure that the machine cannot operate if any safety guard or cover is removed, preventing workers from coming into contact with rotating parts or high-speed spindles, which could lead to serious injuries.
- Weaving Machines: In weaving machines, safety interlocks ensure that the machine will not operate unless all protective covers are in place. This is particularly important as these machines involve high-speed motion, and exposed moving parts could result in injuries. Interlocks can also prevent accidental starts while maintenance or setup activities are being conducted.
- Loom Machines: Loom machines, which are used for weaving fabric, contain a series of rapidly moving parts. Safety interlocking devices are used to stop the machine from operating if a protective cover is open or the system detects that a worker is too close to the moving components. This prevents accidents such as entanglement in the machine’s moving parts.
- Dyeing and Printing Machines: Dyeing and printing machines used in textile production are typically large and involve potentially hazardous chemicals and high temperatures. Safety interlocks ensure that the machine cannot operate unless the system is correctly closed off, preventing accidental exposure to chemicals or heat sources.
- Cutting Machines: Cutting machines used in textiles are often automated and involve sharp blades or rotating knives. Safety interlocks prevent these machines from operating unless safety doors or covers are securely closed, protecting workers from accidental cuts or injuries caused by exposed blades.
- Finishing Machines: These machines are used to process fabrics after they are woven or knitted, including functions such as coating, heat setting, or drying. Safety interlocks prevent the machine from operating if any cover or door is open or if there are any unsafe conditions, such as incorrect alignment or obstruction in the system.
- Carding Machines: Carding machines are used to separate and straighten fibers before spinning. Safety interlocks prevent workers from accessing the machine while it is in operation, as carding involves high-speed rollers that could cause injuries. Interlocks ensure the machine cannot operate unless guards are securely in place.
- Textile Printing Machines: In textile printing, large-scale printing presses and rotary screens are often used. Safety interlocks prevent the machine from starting or running unless all safety measures are in place. These interlocks are important for preventing accidental contact with hot or pressurized surfaces and reducing the risk of burns or mechanical injuries.
- Fabric Inspection Machines: These machines are used to detect flaws in textile fabrics. Safety interlocks ensure that inspection machines cannot operate unless they are fully enclosed, preventing workers from being injured by the machine’s mechanical parts or being exposed to harmful chemicals used during inspection.
- Automatic Fabric Stretching and Wrapping Machines: In automated fabric stretching and wrapping, safety interlocks prevent these systems from operating if the fabric is not securely in place or if maintenance doors are open. This ensures that operators are not exposed to dangerous machinery components.
Key Benefits of Safety Interlocking for Textile Machines
- Enhanced Worker Safety: Safety interlocks are designed to protect workers from the moving parts of textile machines, such as spindles, blades, and conveyor belts. They ensure that machines only operate when it is safe, reducing the likelihood of accidents and injuries. For example, workers are prevented from being exposed to dangerous rotating parts or high-temperature environments.
- Accident Prevention: Safety interlocks are crucial in preventing accidents caused by operator error, such as inadvertently starting a machine while maintenance is being performed or operating machinery without proper safeguards in place. These systems help stop dangerous situations before they can escalate into accidents, such as entanglement or cuts from moving parts.
- Compliance with Safety Regulations: Textile manufacturing is subject to strict safety regulations, such as those from the Occupational Safety and Health Administration (OSHA) or ISO safety standards. Safety interlocking ensures that textile machines meet these safety requirements, reducing the risk of legal issues or non-compliance with local and international regulations.
- Protection of Equipment: Interlocks help protect machines by preventing them from running under unsafe conditions. This can reduce the risk of mechanical breakdowns or failures caused by improper handling, thus extending the lifespan of costly textile machinery and improving long-term cost efficiency.
- Reduced Downtime: Safety interlocks can help reduce downtime by ensuring that machines are operating within safe parameters. Since they prevent accidents and malfunctions, there is less likelihood of system shutdowns due to damage or safety-related issues. As a result, productivity is maximized, and the need for frequent maintenance is minimized.
- Improved Operational Efficiency: By ensuring that safety conditions are met before machine operation, safety interlocks help optimize the overall efficiency of textile production. This leads to fewer interruptions and smoother operations, which increases throughput and reduces bottlenecks in the manufacturing process.
- Reduced Risk of Contamination: In the textile industry, contamination from external sources or improper handling can spoil large quantities of materials. Safety interlocks prevent unauthorized access to the machine and reduce the chance of contamination, ensuring that fabric production maintains its integrity and quality.
- Employee Confidence and Morale: Knowing that safety systems are in place to protect them from potential hazards improves workers’ confidence in the workplace. This can lead to increased morale and productivity, as employees feel safer and more comfortable performing their tasks.
- Cost Savings: By preventing accidents, damage to equipment, and product defects, safety interlocks help reduce the overall cost of operation in textile manufacturing. They contribute to fewer workplace injuries, reduced liability claims, and less frequent equipment repairs, ultimately leading to significant cost savings.
- Minimized Human Error: In automated textile production, human error can lead to costly accidents. Safety interlocks help eliminate human error by automatically ensuring that machines cannot be operated unless all safety protocols are in place. This helps maintain consistent safety standards and prevents mistakes that could result in injury or damage.
Safety interlocking systems are an integral part of textile machine operations, providing essential protection for workers, machinery, and the production process itself. By ensuring that machines operate only when safety conditions are met, these systems reduce the risk of accidents, protect expensive equipment, and ensure compliance with safety regulations. The key benefits of safety interlocking include enhanced worker safety, reduced downtime, improved operational efficiency, and cost savings. In the textile industry, where machines operate at high speeds and involve moving parts, these safety measures are critical for maintaining a safe and productive working environment.