Safety interlocking for Automation Storage Retrieval Systems ( ASRS )
- Home
- Applications
- Door Safety Interlocking
Enquire Now
Let us help you
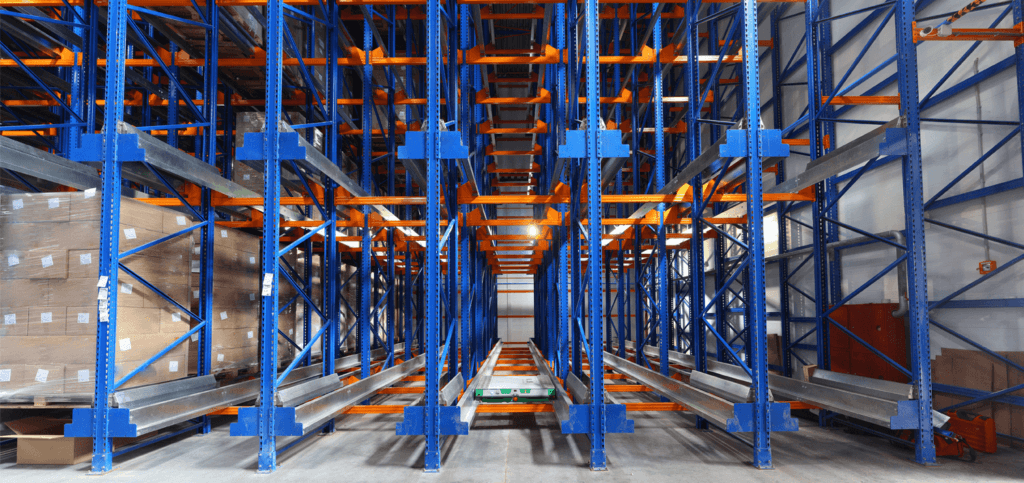
Safety interlocking for Automation Storage Retrieval Systems ( ASRS )
Our sales team has decades of experience in the field finding solutions for our customers’ applications.
- sales@rendertechindia.com
- +91-8698009335
Safety interlocking for Automation Storage Retrieval Systems ( ASRS )
Safety interlocking is a critical feature in Automated Storage and Retrieval Systems (ASRS), which are widely used in warehouses, distribution centers, and manufacturing environments. These systems use automated equipment such as cranes, shuttles, or robotic arms to store and retrieve goods in high-density storage areas. Given the complexity of these systems and the involvement of automated machinery interacting with human operators, safety interlocking is essential to ensure safe operation and to protect both workers and equipment.
What is Safety Interlocking?
Safety interlocking refers to the use of safety switches or mechanisms that prevent machinery or systems from operating unless certain conditions are met. In the context of ASRS, safety interlocks ensure that the automated components only function when it is safe to do so, typically when access doors or safety barriers are closed, or when there is no risk of operator exposure to moving parts.
Applications of Safety Interlocking in ASRS
- Automated Storage Systems: In automated storage, robots or cranes move pallets and bins in a storage area. Safety interlocks ensure that the automated machinery cannot operate if access doors or safety covers are open, reducing the risk of injury to workers who may be near moving parts.
- Conveyor Systems: Conveyor belts in ASRS transport goods between storage locations and sorting areas. Safety interlocks are used to prevent the system from running if safety doors or covers protecting moving parts are not in place. This minimizes the risk of workers being exposed to fast-moving conveyors.
- Stacker Cranes: Stacker cranes, which are used to retrieve and store items in high-rack storage systems, rely on safety interlocks to ensure that the crane does not move unless safety barriers are in place. The interlock system also prevents unauthorized access to areas where cranes are operating.
- Shuttle Systems: Automated shuttle systems, which are used to move items within storage racks, require interlocks to ensure that no one is in the path of the shuttle when it is in operation. Safety mechanisms are triggered to stop movement if someone enters a restricted area.
- Robotic Retrieval Systems: Robotic arms in ASRS may retrieve or store items in highly confined spaces. Safety interlocks prevent the robots from operating if there is a potential for human interaction or unsafe conditions within the workspace.
- Lift Systems: Lift systems in ASRS, which are used to transport goods between different levels of a warehouse, use safety interlocking to ensure the lift does not operate if safety barriers are open or the lift’s access doors are unlatched, reducing the chances of accidents.
- Maintenance and Service Access Points: During maintenance or servicing of ASRS, safety interlocks are used to prevent the system from restarting unexpectedly. This ensures that maintenance personnel can work on the system without being exposed to unintended movement of automated parts.
- Access Control: Safety interlocking systems are often integrated with access control systems, ensuring that only authorized personnel can access specific areas of the ASRS. This restricts entry into high-risk zones where automated equipment is operating, reducing the chance of injury.
Having a safety interlock switch system is essential for two main reasons
- Protecting Operators: The gate setup Pizzato Elettrica- Italy is designed to ensure operators are safe when entering the robot cell. The procedure follows a carefully planned sequence to prevent any safety risks that could arise while the operator is inside. This process keeps the operator protected and minimizes the chance of accidents.
- Minimizing Robot Downtime: Using a locking gate switch along with a “Request Access” button helps control when the robot system stops. This setup ensures that the system halts at a precise moment, which reduces delays. By doing so, we can avoid disrupting the robot’s ongoing tasks, allowing the operator to enter or exit the safe area without losing valuable time.
Key Benefits of Safety Interlocking in ASRS
- Enhanced Worker Safety: Safety interlocks protect workers from moving machinery by ensuring that automated equipment cannot operate unless safety doors, barriers, and safety covers are securely in place. This significantly reduces the risk of injuries, such as being caught in moving parts or exposed to high-speed equipment.
- Prevention of Accidents: Safety interlocking helps prevent a variety of accidents in ASRS environments, such as collisions with automated vehicles, accidental exposure to dangerous moving parts, and injuries caused by improperly secured load handling systems. Interlocks act as a fail-safe to avoid hazardous situations.
- Compliance with Safety Regulations: In many regions, there are strict safety regulations governing the use of automated systems, such as the OSHA (Occupational Safety and Health Administration) and ISO safety standards. Safety interlocks help ASRS installations comply with these regulations, avoiding fines and legal issues while ensuring a safe working environment.
- Improved Operational Efficiency: When safety interlocks are in place, the system is designed to avoid unnecessary downtime caused by accidents or system failures. Machines will only operate under safe conditions, ensuring smooth operation without frequent interruptions, which in turn improves overall system efficiency and throughput.
- Protection of Equipment: Interlocking mechanisms protect equipment from damage by preventing it from operating in unsafe conditions. For instance, automated vehicles, cranes, or shuttles will be prevented from running if there is an obstruction or if access doors are open. This reduces the likelihood of mechanical breakdowns and extends the lifespan of equipment.
- Reduced Maintenance Costs: Since safety interlocks prevent damage to equipment and reduce the frequency of accidents, maintenance costs are lowered. Machines are less likely to suffer from wear and tear caused by unsafe operation, and the system will experience fewer breakdowns, contributing to long-term cost savings.
- Increased Productivity: With safety interlocks ensuring smooth operation, ASRS systems can function without the interruptions that are caused by accidents or mishaps. This leads to an increase in the system’s uptime, which boosts overall productivity. Operators can also work more confidently knowing that safety is ensured.
- Minimized Risk of Contamination: In industries like pharmaceuticals or food manufacturing, contamination is a significant concern. Safety interlocking can help prevent contamination by ensuring that automated systems only operate when all protective measures are in place, preventing unauthorized access to sensitive areas and maintaining clean environments.
- Reduced Risk of Unauthorized Access: Safety interlocking systems can prevent unauthorized personnel from accessing hazardous zones within the ASRS, such as areas where heavy equipment operates or where dangerous moving parts are present. This helps ensure that only trained and authorized personnel can interact with the system.
- Integration with Emergency Shutdown Systems: Many safety interlock systems are integrated with emergency shutdown procedures. In the event of an emergency, the system can be immediately halted, preventing further damage or injury. This integration helps ensure a rapid and effective response to potential safety issues.
Safety interlocking in Automated Storage and Retrieval Systems (ASRS) plays a critical role in maintaining a safe, efficient, and compliant operating environment. By preventing accidents, protecting workers, and ensuring smooth operations, safety interlocks help improve the overall productivity and reliability of these systems. They are essential for reducing downtime, protecting expensive equipment, minimizing risks, and ensuring that automated storage systems function as intended, without exposing workers or equipment to unnecessary hazards. As automation continues to play a larger role in various industries, safety interlocking remains a key component in ensuring that these systems operate safely and efficiently.