Safety interlocking for Warehouse automation
- Home
- Applications
- Door Safety Interlocking
Enquire Now
Let us help you
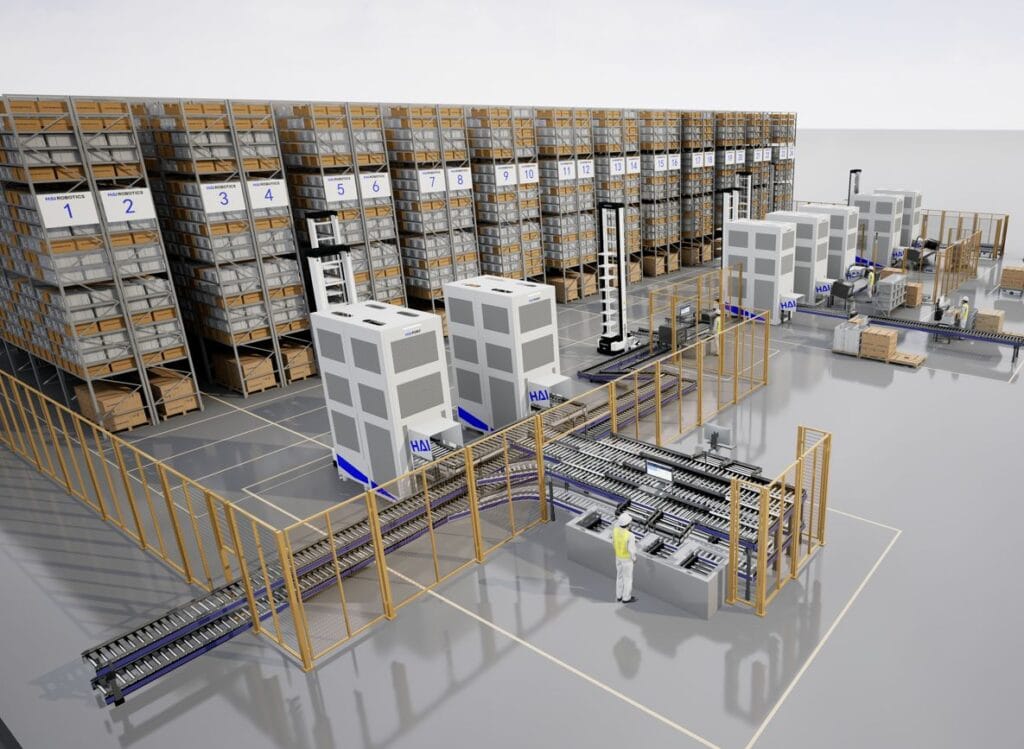
Safety interlocking for Warehouse automation
Our sales team has decades of experience in the field finding solutions for our customers’ applications.
- sales@rendertechindia.com
- +91-8698009335
Safety interlocking for Warehouse automation
Safety interlocking plays a crucial role in warehouse automation systems, which rely on automated equipment like robotic arms, conveyor belts, automated guided vehicles (AGVs), and storage/retrieval machines to move goods efficiently. These automated systems significantly enhance warehouse operations but introduce new risks due to the interaction between humans and machines. Safety interlocking systems ensure that these systems function safely, preventing accidents and injuries by only allowing operations to occur under safe conditions.
What is Safety Interlocking?
Safety interlocking refers to the mechanism that ensures automated equipment in a warehouse cannot operate unless safety protocols are followed. Interlocks are typically used with safety devices, such as doors, gates, or barriers, and are designed to stop the machine or system from running when these safety conditions are not met. For example, the operation of a robot or conveyor might be stopped if a protective door is open or a sensor detects that a worker is in a danger zone.
Applications of Safety Interlocking in Warehouse Automation
- Automated Guided Vehicles (AGVs): AGVs are commonly used in warehouses to transport goods between locations. Safety interlocks ensure that these vehicles cannot move unless all access points are clear and the system is in a safe operational state. They prevent accidents by stopping the AGV if a worker enters the vehicle’s path or if safety barriers are not in place.
- Conveyor Systems: Conveyors in automated warehouses move goods between storage locations and sorting areas. Safety interlocks in conveyor systems ensure that if any protective cover or access door is open, the conveyor will stop. This prevents workers from coming into contact with fast-moving parts, minimizing the risk of injury.
- Automated Storage and Retrieval Systems (ASRS): In ASRS, automated cranes, shuttles, or robotic arms store and retrieve goods. Safety interlocks ensure these machines do not operate if doors are open, access barriers are not secure, or if human workers are in the vicinity of moving parts. This helps prevent collisions, crush injuries, and other accidents.
- Robotic Arms and Pick-and-Place Systems: Robotic arms are used in warehouses for picking and placing items. Interlocking mechanisms prevent the robots from functioning if safety barriers are not in place or if an operator is too close to the robot’s operating area. This safeguards workers from potential harm while enabling efficient automation.
- Automated Palletizing Systems: Palletizing robots automate the process of stacking goods onto pallets. Safety interlocks are used to ensure that the palletizer cannot operate if safety doors are open or if the area is not clear of people. This prevents accidents where workers could be accidentally caught in the automated stacking process.
- Automated Sorting Systems: Automated sorting systems are used to classify and direct goods to their appropriate storage or shipping locations. Safety interlocks help ensure that the sorting systems cannot operate unless the system is securely enclosed and free from human interference.
- High-Rack Storage Systems: In high-rack systems, goods are stored at high levels, and automated cranes or shuttles retrieve items. Safety interlocking ensures that the crane or shuttle can only move when access doors are properly closed and when the system is clear of obstacles. This prevents mishaps, particularly in areas where machines operate at high speeds.
- Loading and Unloading Robots: Automated systems that load and unload goods from trucks or containers benefit from safety interlocking systems that prevent the machine from operating unless safety conditions are met, such as the door of the container being securely closed or the area being clear of personnel.
- Human-Machine Interface (HMI) Safety Features: Warehouse automation often includes interfaces where operators monitor and control automated systems. Safety interlocks integrated with these systems ensure that operators cannot manually override safety features unless it is safe to do so, preventing human error that could lead to accidents.
Key Benefits of Safety Interlocking in Warehouse Automation
- Enhanced Worker Safety: The primary benefit of safety interlocks in warehouse automation is the protection of workers. By ensuring that automated machinery cannot operate when access doors are open, or when workers are in a hazardous zone, safety interlocks minimize the risk of injury from moving parts, machinery collisions, or automated vehicles.
- Accident Prevention: Safety interlocking systems prevent accidents in automated warehouses by automatically stopping machinery when a potential safety hazard is detected, such as a worker entering a danger zone or a safety door being left open. This reduces the likelihood of collisions, crush injuries, and other incidents caused by human error or equipment malfunctions.
- Compliance with Safety Regulations: Automated warehouses must comply with strict safety standards and regulations (such as OSHA and ISO safety guidelines). Safety interlocks ensure that automated systems meet these regulatory requirements, reducing the risk of penalties or safety violations and promoting a safe work environment.
- Protection of Expensive Equipment: Safety interlocks help prevent damage to expensive equipment by stopping the machinery if an unsafe condition is detected. For example, interlocks prevent automated systems from running if access doors are open or if equipment is malfunctioning, which helps reduce the risk of costly repairs or system downtime.
- Reduced Downtime and Maintenance Costs: Interlocking systems reduce downtime by ensuring that automated systems only operate in safe conditions, preventing equipment damage or system malfunctions caused by unsafe operations. This leads to fewer breakdowns and maintenance issues, ultimately lowering the cost of repairs and increasing the longevity of the equipment.
- Increased Operational Efficiency: When safety interlocks are in place, systems run more reliably. Workers are less likely to be injured, and there are fewer disruptions due to accidents or equipment malfunctions. This boosts overall productivity and helps ensure that warehouse automation systems run smoothly, contributing to higher throughput and efficiency.
- Improved Process Control: Interlocking mechanisms contribute to better control over warehouse automation processes. Automated systems only function when the environment is safe, which helps prevent errors, inconsistencies, or accidents caused by operating in unsafe conditions. This results in smoother and more reliable operations.
- Reduced Risk of Liability and Insurance Costs: By preventing accidents and improving worker safety, safety interlocks reduce the risk of liability claims and compensation costs. This also helps reduce warehouse operators’ insurance premiums by demonstrating a commitment to safety and reducing the likelihood of workplace injuries.
- Minimized Risk of Contamination: In industries like pharmaceuticals or food manufacturing, contamination risks are a critical concern. Safety interlocks ensure that automated systems operate only under controlled conditions, preventing access to sensitive areas or reducing the chance of contamination in storage and sorting processes.
- Better Worker Confidence and Morale: When workers know that safety measures are in place and that the system is designed to prevent accidents, they are more likely to feel confident and secure in their working environment. This leads to higher employee morale and satisfaction, which can improve performance and reduce turnover rates.
Safety interlocking systems are a vital part of warehouse automation, ensuring that equipment operates safely and efficiently while minimizing risks to workers and reducing the likelihood of costly accidents. These systems help prevent machinery from operating under unsafe conditions, protect employees from injuries, ensure compliance with safety regulations, and safeguard expensive equipment. By implementing effective safety interlocks, warehouse operators can enhance productivity, reduce downtime, and create a safer working environment, ultimately contributing to the long-term success of the automated warehouse system.